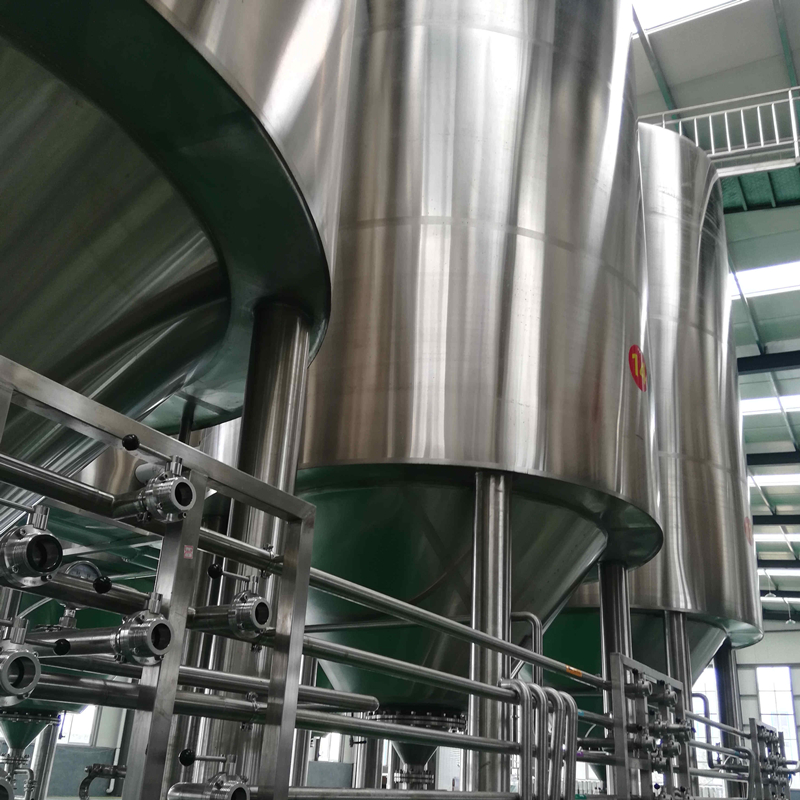
15000L (150HL) Commercial beer brewing System product advantage:
1.WEMAC supply beer brewing system with turn-key project.
2.WEMAC provide beer equipment with free consultation,3D design,free installation,training.
3.Three years warranty for the main equipment and spare parts.
4.WEMAC beer machine brew different flavors of beer and brew several flavors of beer at the same time.
5.WEMAC beer machine has beautiful appearance, it is convenient for customer visiting.
15000L (150HL) Commercial Beer Brewing System application scope
Regional breweries, modern breweries and industrial breweries
15000L (150HL) Commercial Beer Brewing System basic information
Output capacity:15000L(150HL)
Heating method:steam or direct fire;
Power supply:
Single Phase/ 220(110, 240…)v/50(60)Hz
3phase/380(220, 415,440…)v/50 (60)Hz
A 15,000-liter (or 150-hectoliter) commercial beer brewing system refers to the capacity of the brewing equipment used in a commercial brewery. It indicates the maximum volume of beer that can be produced in a single batch. Here's an overview of such a brewing system:
Brewhouse: The brewhouse is the core component of the brewing system where the beer production process takes place. It typically consists of several vessels:
Mash/Lauter Tun: This vessel is used for mashing and lautering processes, where the crushed grains are mixed with hot water to extract fermentable sugars.
Brew Kettle/Whirlpool: The brew kettle is used for boiling the wort (sugar-rich liquid extracted from the mash). It also serves as a whirlpool vessel to separate hop and trub sediment from the wort.
Hot Liquor Tank: This tank stores hot water used in various brewing processes.
Fermentation: After boiling, the wort is transferred to fermentation vessels, where yeast is added to convert the sugars into alcohol and carbon dioxide. In a commercial brewery, multiple fermentation vessels are used, usually made of stainless steel or conical in shape.
Conditioning and Maturation: Once fermentation is complete, the beer may undergo a conditioning and maturation phase. This step allows flavors to develop and any remaining sediment to settle. It can take several weeks or months, depending on the beer style.
Filtration and Packaging: After conditioning, the beer is typically filtered to remove any remaining particles. It can then be packaged into kegs, bottles, or cans, depending on the brewery's preference and distribution strategy.
It's important to note that the brewing system mentioned above is a general description, and the specific configuration may vary depending on the brewery's requirements, brewing techniques, and available technology. Commercial breweries often have additional equipment for yeast propagation, temperature control, quality control, and other specialized processes.
Milling system | Stainless steel or carbon steel malt mill |
Mash system | Material:SUS316L, SUS304,copper; |
Fermentation system | 15000L(150HL) / 30000L(300HL)fermentation tank |
Yeast breeding system | Two -stage |
CIP | Mobile or Fixed CIP |
Energy system | Heating system &cooling system design capacity meet the requirement |
Electric system | Stainless steel electric cabinet with imported brand PLC and touch screen or spraying plastics electric cabinet with push-button |
Pipeline fittings | Including mash line, alcohol water line and other system line,valves |
Filtering and sterilization system | Candle type diatomite filter and pasteurizer |
| To bar wine column |
Here are some additional details and considerations when using a 15,000 liter (or 150 hectare liter) commercial beer brewing system:
System capacity: The 15,000-liter brewing system belongs to medium and large-scale commercial brewing equipment, which is suitable for medium-scale commercial beer production. Such a system can brew large quantities of beer at once and is suitable for bars, restaurants, small breweries or medium-sized brewing enterprises.
Automated controls: Large-scale commercial brewing equipment is often equipped with highly automated control systems to ensure the accuracy and consistency of the production process. Temperature, pressure, time and other key parameters can be monitored and adjusted through an automated control system.
Raw material requirements: A 15,000 liter brewing system needs a lot of raw materials to make beer. This includes a lot of malt, hops, yeast and water. Commercial wineries usually establish long-term cooperative relationships with suppliers to ensure a stable supply of raw materials.
Energy Consumption: Large-scale brewing systems require large amounts of energy to heat and cool liquids. This includes steam or natural gas for wort heating and boiling, and electricity for cooling and temperature regulation.
Sanitation and Cleanliness: Commercial brewing systems require stringent sanitation and cleaning measures to ensure hygienic standards during the brewing process. It is critical to regularly clean and sanitize brewing equipment to avoid the buildup of bacteria or other contaminants.
Personnel requirements: Large brewing systems require experienced brewers and brewing teams to operate and supervise. They should be familiar with the winemaking process, fermentation control, hygiene standards and quality control.
Expansibility: A 15,000-liter brewing system has a certain expansion potential and can be expanded according to the needs of the winery. This means that the brewing system can add additional fermenters, batching systems or other additional equipment to meet increasing production requirements.
Technical support and maintenance: Large commercial brewing systems often require professional technical support and regular maintenance to ensure the normal operation and performance of the equipment. Brewers usually establish long-term cooperative relationships with suppliers to obtain timely technical support and maintenance services.
Market demand and distribution: Using a 15,000 liter brewing system means you have the capacity to produce large quantities of beer. Before starting to invest, it is important to understand market demand and distribution channels. Make sure you have proper channels to sell and distribute your products such as restaurants, bars, supermarkets, distributors and direct sales etc.
Cost and Return on Investment: A large commercial brewing system is an expensive investment. Before buying, assess the size of your winery, market demand and expected production to ensure a reasonable return on your investment.
In summary, a 15,000 liter commercial beer brewing system provides medium-sized breweries with the ability to produce large volumes of beer. Such systems involve complex processes, automation controls, material management and human resources. At the same time, successfully running a commercial winery also needs to consider commercial factors such as market demand, distribution channels and return on investment.
If you have more specific questions about specific brewing equipment, brewing processes, or other related topics, please feel free to ask.
If you have more specific questions about commercial brewing systems or the brewing process, feel free to ask!
If you want to ask anything just fill in the form below and send us.